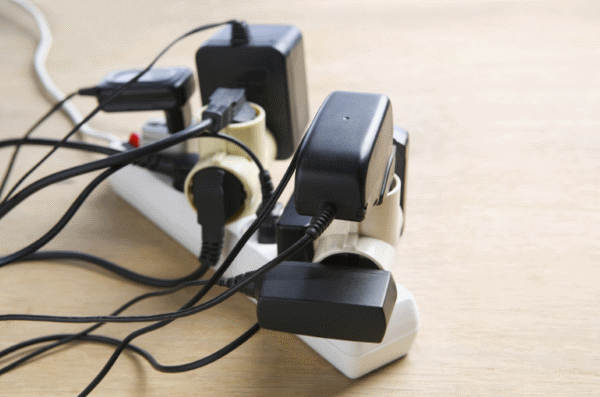
The much needed harmonisation really doesn’t offer us that much harmony when it comes to Electrical Safety!
Although Australia is one nation, we currently have different test and tag legislation across Australia.
Legislation in most states is comparable; however as the Testing and Tagging regulations in QLD differ so greatly from the rest of the country, the Queensland rules deserve an article of their own.
In fact, Queenslanders noticed no change in the area of Electrical safety when the model Workplace Health and Safety legislation was implemented in January 2012.
QLD electrical safety legislation continued to over-ride the Workplace Health and Safety legislation and they therefore continue to face the same dilemmas when conducting business across state borders. QLD legislation in this area is driven by the QLD Electrical Safety Act 2002 and QLD Electrical Safety Regulations 2013. The QLD legislation is highly prescriptive, with a number of key differences vs the other states.
The key areas of difference are Licensing, Training, Repairs, and the different testing requirements for different Classes of Work.
Licensing and Training
I recently attended a seminar put on by the QLD Electrical Safety Office centered on licensing. It was refreshing to see a Government department so actively keen to explain the way their legislation worked, and the presentation put on by the QLD Electrical Safety Office was clear, concise and easy to understand.
In saying that, there was a definite “don’t shoot the messenger” attitude towards some of the more difficult questions raised by attendees which really could have provided the Electrical Safety Office with excellent feedback on the way safety legislation is actually being implemented in real life.
In QLD, an employee of an organisation who has been deemed competent by their employer can complete testing and tagging for their organisation. There are no special courses to complete, and no special licences to hold. However, should that same person wish to offer test and tag services to another organisation (of which he is not an employee) and wish to profit from providing that service, the person will need to have completed a Nationally recognised Test and Tag course, and hold a Restricted QLD Electrical Contractors licence.
Some may argue that this creates a large “barrier to entry” and that only dedicated professionals will bother to jump though these hoops to establish a business. The Nationally recognised course (UEERL0003) is a good course, and I firmly believe that regardless of your State of operation that this is the course any technician wishing to offer this service should complete. However, like most courses of an 8 hour duration, there is limited practical component.
In my experience, 2 weeks in depth practical training on testing and tagging should be the minimum amount of training undertaken – along with the expectation of a very steep learning curve for at least 6 months!
The more difficult component is licensing. Any one that has secured a QLD Electrical Contractors license (restricted or otherwise) will tell you just completing the form is a challenge! There are both Business Management and Technical components to address, and additional management courses to complete if you cannot validate your business experience. Consumer Protection Insurance is also required in addition to your Public Liability Insurance.
These annual Licensing costs are not applicable in any other State, and I wonder whether the holding of a license makes the technician any more competent in providing a Test and Tag service?
Minor Repairs to Plugs and Sockets
If you wander in to the Electrical section of your local hardware store you will see rows and rows of Plugs and Sockets for sale. I certainly don’t see too many Electricians buying them, and can only assume that the constant spruiking from Electrical Safety state regulators imploring the general public to refrain from completing their own electrical work appears to be falling on deaf ears.
In all states (excl QLD) persons who have been deemed competent are permitted to replace plugs and sockets of portable electrical equipment as part of their business service offering. They are not deemed competent to install hot water services, nor fix GPO’s, nor install lighting. They are simply deemed competent enough to replace a faulty plug with a new one or repair a plug that may be loose with exposed conductors. Competent technicians then confirm the repair has been completed correctly by testing the appliance with a Portable Appliance Tester, and then return the safe item to service.
In QLD, despite the local hardware store still stocking the same volumes of plugs and sockets (and therefore the assumption that the general public in QLD are also dangerously completing their own illegal electrical work), competent persons are not permitted to replace plugs and sockets regardless of whether the item is tested before it is returned to service. Interestingly, the local plumber is permitted to apply for a Restricted Electrical licence in QLD in order to connect a hot water service, but a competent person charged with the responsibility of ensuring the safety of appliances is not permitted to even change a plug top!
In my experience, items that have failed testing and removed from service regularly find their way back in to service within a matter of days. They could have bright red flashing neon lights on them saying “DANGER” but experience tells me they still get used by a staff member who believes “it looks OK” and then subsequently receives an electric shock from a faulty plug top.
According to the QLD Electrical Safety office, Test and Tag technicians in the state of QLD are simply responsible for alerting the workplace to the failed items and then removing them from service. What happens to those items once the technician has left site is then the responsibility of the Client. It does raise the question – is this section of the Electrical Safety Act really doing all it can to ensure workplace safety?
But I have an RCD!
Whilst any Electrician worth his salt knows that an RCD is not the be all and end all for Electrical Safety, they also know that RCD’s have and will continue to save lives.
Quite rightly, the QLD Electrical Safety regulations stipulate the installation of fixed RCD’s in all Manufacturing environments. However, the Regulations also state that if you have RCD’s protecting every circuit of your Office then you are not required to complete Testing and Tagging on any of your portable electrical appliances.
With the ability to seemingly work from anywhere (as I write I am in a remote part of Victoria typing on a laptop with not one RCD in sight!), along with the blurring of our work and personal lives, business could be leaving itself open should an employee receive an electric shock from a portable electrical appliance outside of the traditional workplace.
There is a reason for all this legislation in QLD. If you go back in history, QLD had the worst electrical safety record in our country. The statistics have improved, but there is still a way to go. Whilst we are supportive of, and can see the benefits of licensing for Testing and Tagging, the fact that suitably trained and competent technicians cannot complete minor repairs is clearly a failure in the current legislation that must be addressed.
Get a free quote
"*" indicates required fields